بخش اول :
جهت کسب اطلاعات بیشتر در این زمینه، بخش بعدی را مطالعه کنید.
مقدمه
در دنیای صنعت، جایی که تأمین انرژی حرارتی نقش حیاتی در تداوم فرآیندهای تولیدی و بهرهوری عملیاتی دارد، حضور یک سیستم قدرتمند و قابلاعتماد برای تولید بخار، غیرقابل چشمپوشی است. دیگ بخار یا بویلر، بهعنوان قلب تپنده سیستمهای بخار، وظیفهی تبدیل آب به بخار در شرایط کنترلشده و تحت فشار را برعهده دارد و در طیف وسیعی از صنایع، از بیمارستانها گرفته تا نیروگاههای بزرگ، نقشی کلیدی ایفا میکند. اهمیت انتخاب نوع صحیح دیگ بخار چه فایرتیوب باشد و چه واترتیوب تنها به مسئله ظرفیت یا فضای نصب محدود نمیشود؛ بلکه عملکرد بهینه، مصرف انرژی، سهولت نگهداری و حتی سلامت تجهیزات جانبی مانند مبدلها و لولهها را نیز تحت تأثیر قرار میدهد.
در این میان، درک تفاوتهای فنی میان انواع دیگهای بخار، آشنایی با مزایا و معایب ساختارهای مختلف مانند مدلهای عقب مرطوب، عقب خشک یا شعله برگشتی، و همچنین آگاهی از اهمیت بهکارگیری تجهیزات جانبی ضروری مانند سختیگیر، میتواند منجر به طراحی سیستمی هوشمند و کارآمد شود که هم در زمان و هم در هزینهها صرفهجویی کرده و عمر مفید تجهیزات را افزایش دهد. مقاله پیشرو، با نگاهی جامع و تحلیلی، به بررسی این ابعاد حیاتی از سیستمهای دیگ بخار پرداخته و راهنمایی مفید برای مهندسان، طراحان و بهرهبرداران صنعتی خواهد بود.
دیگ بخار؛ قلب تپنده سیستمهای حرارتی با بخار
دیگ بخار یا به تعبیر دقیقتر، مولد بخار، دستگاهی بسته است که در آن آب تحت فرآیندی کنترلشده به بخار با فشاری بالاتر از فشار جو تبدیل میشود. این بخار در بسیاری از فرآیندهای صنعتی، گرمایشی و تولید انرژی، نقش اصلی را ایفا میکند و بههمین دلیل، طراحی و انتخاب نوع مناسب دیگ بخار از اهمیت بالایی برخوردار است.
طبقهبندی دیگهای بخار بر اساس ساختار عملکردی
دیگهای بخار را میتوان بر اساس نحوه تبادل حرارت و عبور سیال، به دو دسته کلی تقسیم کرد:
1. دیگ بخار آب در لوله (Water Tube Boiler)
2. دیگ بخار آتش در لوله (Fire Tube Boiler)
هرکدام از این دو نوع، ویژگیها و کاربردهای خاص خود را دارند که بر اساس ظرفیت مورد نیاز، فشار عملیاتی و نوع فرآیند، در صنایع مختلف مورد استفاده قرار میگیرند.
ظرفیت دیگ بخار؛ معیاری از کارایی عملیاتی
ظرفیت یک دیگ بخار معمولاً بر اساس میزان آبی سنجیده میشود که در بازه زمانی یک ساعت به بخار تبدیل میگردد. این شاخص تعیینکننده، معیاری مهم در طراحی سیستمهای بخار و انتخاب بویلر مناسب با نیاز حرارتی پروژه است.
دیگ بخار آب در لوله (Water Tube Boiler)
در این نوع بویلر، سیال اصلی یعنی آب، از درون لولههایی عبور میکند که میان درامهای بالا و پایین متصل شدهاند. حرارت حاصل از احتراق سوخت در کوره، از طریق تابش مستقیم و نیز جریان همرفتی گازهای داغ به لولهها منتقل شده و موجب تبخیر آب درون آنها میشود. این ساختار، امکان تولید بخار با ظرفیت بالا و فشارهای بسیار زیاد را فراهم میکند.
کاربردها :
این نوع دیگ بخار بیشتر در محیطهایی استفاده میشود که تولید مداوم و حجیم بخار مورد نیاز است؛ مانند نیروگاههای تولید برق، پالایشگاههای نفت و گاز، و صنایع سنگین که به فشارهای عملیاتی بالا نیاز دارند.
دیگ بخار آتش در لوله (Fire Tube Boiler)
در این سیستم، احتراق درون محفظهای بسته موسوم به کوره رخ میدهد و گازهای داغ حاصل از این احتراق، از درون لولههایی عبور میکنند که در داخل محفظهای پر از آب قرار دارند. حرارت از طریق دیواره این لولهها به آب منتقل شده و باعث تبدیل آن به بخار میشود. این دیگها معمولاً دارای چند مسیر (پاس) هستند که در افزایش راندمان حرارتی بسیار مؤثر است.
کاربردها :
بویلرهای فایرتیوب بیشتر در صنایع متوسط و سبک کاربرد دارند؛ از جمله در صنایع غذایی، بیمارستانها، صنایع قند و کارخانههای تولید لاستیک. در این مکانها، فشار بخار متوسط و بهرهبرداری ساده، جزو اولویتهاست.
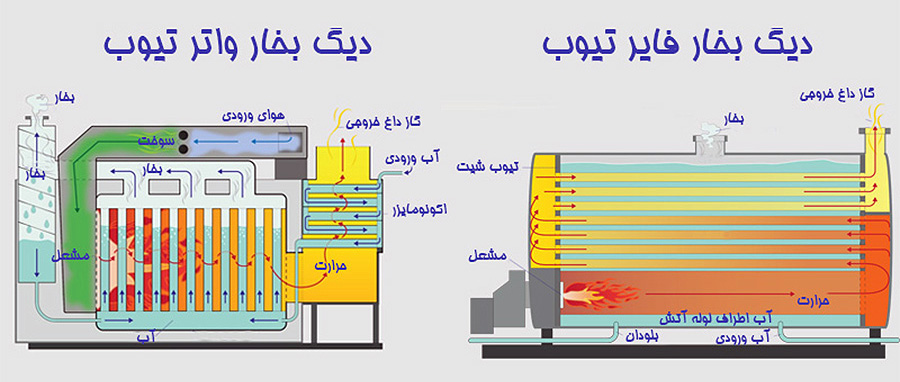
طبقهبندی دیگهای فایرتیوب بر اساس ساختار و عملکرد
دیگهای فایرتیوب یا آتش در لوله ، یکی از پرکاربردترین انواع دیگهای بخار در صنایع مختلف محسوب میشوند. این نوع دیگها را میتوان از جنبههای مختلفی تقسیمبندی کرد که در ادامه به تفصیل بررسی میشوند.
تقسیمبندی براساس وضعیت نصب : افقی یا عمودی
نخستین دستهبندی دیگهای فایرتیوب بر مبنای جهت نصب بدنه صورت میگیرد. این دیگها یا بهصورت افقی طراحی میشوند یا به شکل عمودی :
• دیگ فایرتیوب افقی : رایجترین نوع در صنایع است. به دلیل بهرهبرداری آسان، راندمان بهتر و نگهداری سادهتر، در ظرفیتهای بالا ترجیح داده میشود.
• دیگ فایرتیوب عمودی : بیشتر در فضاهای محدود یا ظرفیتهای پایین مورد استفاده قرار میگیرد. ساختار سادهتر و حجم کمتری دارد.
تقسیمبندی براساس تعداد پاسهای عبور دود
عملکرد حرارتی دیگ فایرتیوب به مسیر عبور گازهای داغ وابسته است. بر این اساس، این دیگها معمولاً به دو نوع کلی تقسیم میشوند :
• دو پاس (Two Pass) : گازهای داغ فقط دو مسیر رفتوبرگشت را طی میکنند. در مقایسه با مدلهای پیشرفتهتر، بازده پایینتری دارد.
• سه پاس (Three Pass) : طراحی بهینهتری دارد که در آن گازهای احتراق سه مسیر مجزا را طی میکنند و این باعث افزایش انتقال حرارت و راندمان بالاتر میشود.
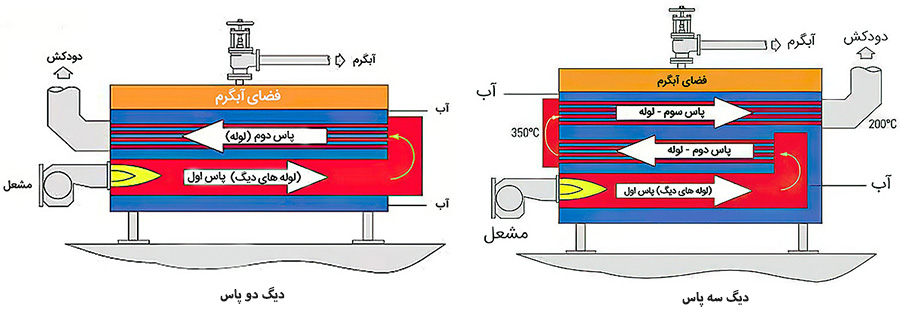
انواع دیگ فایرتیوب افقی بر اساس طراحی ناحیه برگشت
در میان دیگهای فایرتیوب افقی، ساختار ناحیه برگشت حرارت اهمیت زیادی دارد. بر اساس نوع طراحی این بخش، چهار مدل اصلی وجود دارد :
1. دیگ عقب مرطوب (Wet Back)
در این مدل، محفظه برگشت گازهای داغ کاملاً درون بخش پر از آب قرار دارد. پس از ورود گازهای احتراقی از کوره به این ناحیه، آنها وارد لولههای پاس دوم و سپس پاس سوم میشوند. چنین طراحیای باعث افزایش راندمان، کاهش اتلاف حرارتی و بهینهسازی مصرف سوخت میشود. معمولاً در ظرفیتهای بالا (۳ تن بخار به بالا) مورد استفاده قرار میگیرد.
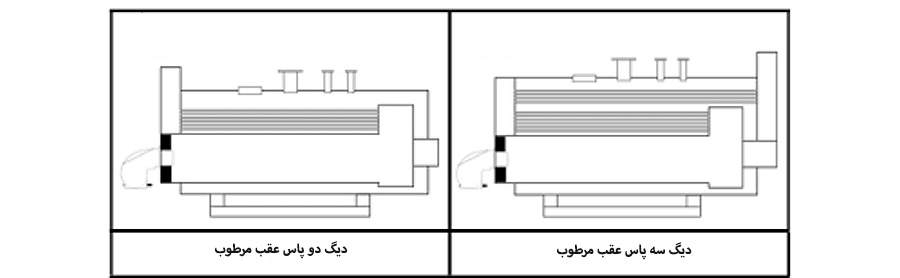
2. دیگ عقب خشک (Dry Back)
برخلاف مدل مرطوب، محفظه برگشت در این نوع دیگ در تماس مستقیم با آب نیست و معمولاً از مصالح نسوز مانند بتن ساخته میشود. این ساختار منجر به راندمان پایینتر و استهلاک بالاتر دستگاه میگردد. همچنین عملیات تعمیر و نگهداری در این مدل، پیچیدهتر و پرهزینهتر است.
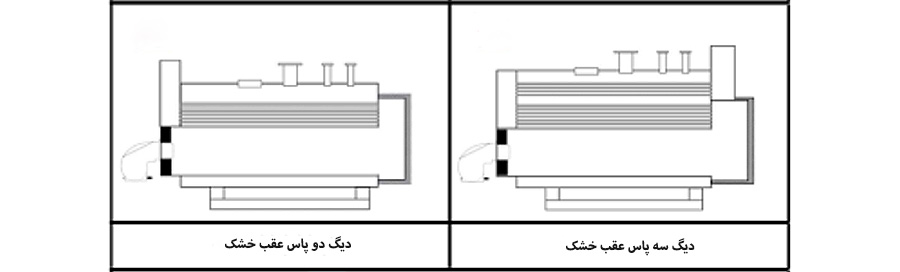
3. دیگ شعله برگشتی (Reverse Fired)
در این نوع طراحی، مشعل در یک کوره بزرگ قرار میگیرد و شعله تولیدشده پس از برخورد با انتهای کوره، مسیر خود را برعکس کرده و از اطراف مشعل وارد لولههای عبور دود میشود. این روش باعث تمرکز بالای حرارت در یک ناحیه مشخص میشود و برای فرآیندهایی که به گرمایش متمرکز نیاز دارند، انتخاب مناسبی است.
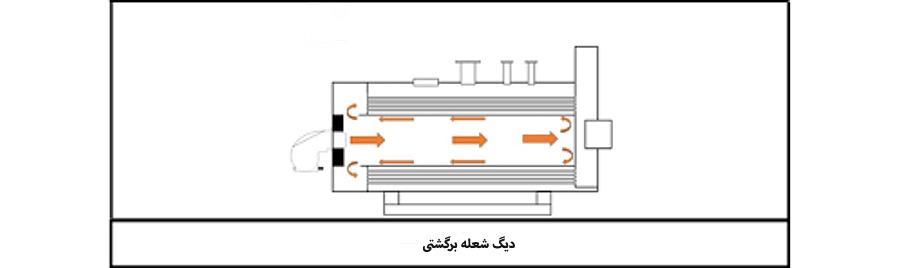
4. دیگ عقب نیمه مرطوب (Semi Wet Back)
این مدل ترکیبی از ساختار عقب خشک و مرطوب است. بخشی از محفظه برگشت در تماس با آب قرار میگیرد، اما نه بهصورت کامل. این مدل سعی دارد تا تعادل بین هزینه ساخت، راندمان و تعمیرپذیری را برقرار کند.
انتخاب نوع دیگ فایرتیوب باید با در نظر گرفتن شرایط عملیاتی، ظرفیت مورد نیاز، فضای نصب و هدف نهایی صورت گیرد. توجه به جزئیات طراحی میتواند تفاوت چشمگیری در عملکرد، طول عمر، و مصرف انرژی سیستم حرارتی ایجاد کند.
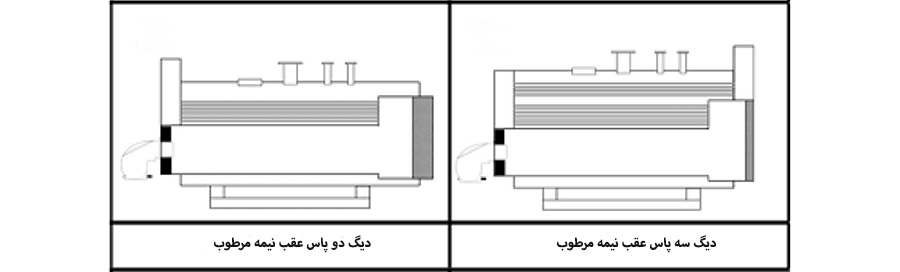
سختیگیر؛ کلید سلامت و راندمان دیگ بخار
یکی از حیاتیترین بخشهای جانبی که عملکرد و دوام دیگ بخار را تضمین میکند، سختیگیر آب است. این تجهیز وظیفه دارد که یونهای کلسیم و منیزیم موجود در آب را حذف کند؛ دو عنصری که اگر در سیستم باقی بمانند، تبدیل به دشمن پنهانی برای دیگ خواهند شد.
چرا باید سختیگیر استفاده کنیم؟
آب بدون تصفیه، بهویژه در مناطقی که سختی آب بالاست، وقتی وارد دیگ بخار میشود، با بالا رفتن دما شروع به رسوبگذاری در دیوارهها و لولههای دیگ میکند. این رسوبات دقیقاً مثل جرم داخل یک کتری خانگی عمل میکنند اما با تبعات سنگینتر :
• باعث کاهش سطح تماس موثر بین آب و لولههای حرارتی میشوند.
• مانع انتقال مؤثر گرما به آب شده و بهرهوری انرژی را به شدت پایین میآورند.
• برای جبران این اتلاف، سیستم مجبور به مصرف سوخت بیشتر میشود تا فشار بخار کافی تولید شود.
هزینههای پنهان عدم استفاده از سختیگیر
فرآیند رسوبزدایی از دیگ بخار نهتنها هزینهبر است، بلکه باعث توقف خطوط تولید، از بین رفتن راندمان، و استهلاک زودهنگام تجهیزات هم میشود. این یعنی عدم استفاده از سختیگیر میتونه منجر به ضرر مالی، افزایش مصرف انرژی و کاهش عمر مفید تجهیزات بشه.
یک گام پیشگیرانه، یک عمر عملکرد بهینه
نصب سختیگیر در ورودی دیگ بخار، نه فقط یک انتخاب فنی، بلکه یک سرمایهگذاری استراتژیک روی عملکرد پایدار و بدون دردسر سیستم است. با تصفیهی اولیهی آب، دیگ بخار نفس راحتی میکشد و شما نیز از هزینههای اضافی در امان خواهید بود.
نتیجهگیری
همانطور که در این نوشتار بررسی شد، دیگ بخار فراتر از یک تجهیز ساده حرارتی، نقشی حیاتی در پایداری، راندمان و ایمنی فرآیندهای صنعتی ایفا میکند. شناخت دقیق تفاوتهای عملکردی میان انواع بویلرها و ساختارهای طراحی آنها (مانند فایرتیوب افقی سهپاس یا مدلهای واترتیوب با فشار بالا)، امکان انتخابی هدفمند و متناسب با نیاز پروژه را فراهم میسازد. همچنین، غفلت از جزئیات ظاهراً ساده اما حیاتی مانند انتخاب صحیح سختیگیر، میتواند تبعات سنگینی از جمله افزایش مصرف سوخت، کاهش راندمان، فرسودگی زودهنگام و حتی آسیب جدی به کل سامانه بهدنبال داشته باشد.
در نهایت، سرمایهگذاری در طراحی علمی سیستم بخار چه از منظر انتخاب نوع بویلر، چه در بحث نگهداری و بهرهبرداری نهتنها بازده انرژی را به شکل چشمگیری افزایش میدهد، بلکه با کاهش هزینههای پنهان تعمیرات و توقفات احتمالی، مسیر بهرهبرداری پایدار و مطمئن از خطوط تولید را هموار میسازد. بویلر مناسب، با طراحی دقیق و تجهیزات جانبی هوشمند، یک تضمین بیصدا اما قاطع برای تداوم انرژی در هر واحد صنعتی است.