بخش دوم:
جهت کسب اطلاعات بیشتر در این زمینه، بخش قبلی را مطالعه کنید.
مقدمه
در قلب هر سیستم بخار، عنصری حیاتی به عنوان آب تغذیه دیگ بخار وجود دارد که گاه نادیده گرفته میشود. کیفیت این آب، نهتنها در عملکرد بویلر تأثیر مستقیم دارد، بلکه میتواند مرز میان یک سیستم کارآمد و یک ساختار پرهزینه و آسیبپذیر باشد. برخلاف تصور عموم، پاکی ظاهری آب معیار مناسبی برای تزریق آن به دیگ بخار نیست؛ بلکه بررسی دقیق شاخصهای شیمیایی، فیزیکی و حرارتی، نقش کلیدی در پیشگیری از خوردگی، رسوبگذاری، افت راندمان و حتی خطرات ایمنی ایفا میکند.
از حذف یونهای سختکننده با کمک رزینهای کاتیونی در سختیگیرها گرفته تا فرآیندهای هواگیری با دیاِریتور و استفاده از تجهیزات مدرنی مانند سوپرهیتر و اکونومایزر، هر بخش از سیستم بخار برای رسیدن به حداکثر بازدهی، نیازمند نوعی تعامل دقیق با کیفیت آب ورودی است. در این میان، طراحی مناسب لولهکشی، مدیریت بازگشت کندانسیت و استفاده از منابع انرژی جایگزین یا بازیافتی، بهمنزلهی تکمیل یک چرخهی هوشمند در تولید و مصرف بخار خواهد بود. شناخت کامل از ویژگیهای آب تغذیه و تعامل آن با ساختارهای فنی دیگ بخار، یکی از الزامات غیرقابلچشمپوشی برای مهندسان و طراحان سیستمهای حرارتی است؛ دانشی که میتواند هم بهرهوری را افزایش دهد و هم هزینههای عملیاتی را بهصورت چشمگیر کاهش دهد.
معرفی دیگ بخار و اصول طراحی
دیگهای بخار بهعنوان یکی از اجزای حیاتی سیستمهای حرارتی صنعتی، معمولاً مطابق با آییننامهها و استانداردهای فنی معتبر از جمله دستورالعملهای انجمن مهندسین مکانیک آمریکا (ASME) طراحی و ساخته میشوند. دلیل این الزام، عملکرد این تجهیزات در فشارهایی بهمراتب بالاتر از فشار جو است که مستلزم رعایت استانداردهای ایمنی و فنی دقیق میباشد. تعیین ظرفیت دیگ بخار در یک پروژه معمولاً ترکیبی از عوامل مختلفی است؛ از جمله نیاز تجهیزات فرآیندی، گرمایش مستقیم، تلفات حرارتی شبکه و بخار مورد نیاز برای فاز راهاندازی سیستم.
شاخصهای انتخاب دیگ برای پروژههای کوچک و بزرگ
در پروژههای حرارتی کوچکتر، معمولاً ظرفیت موردنیاز بر اساس بار خالص محاسبه میشود؛ به این معنا که فقط بخار مورد استفاده مستقیم در نظر گرفته میشود. اما در مقیاسهای بزرگ صنعتی یا پروژههایی با بارهای متغیر و پیچیده، معیار انتخاب بر اساس ظرفیت ناخالص انجام میشود که شامل تمام افتها، تلفات و ذخایر اطمینان نیز هست. یکی از نکات کلیدی در طراحی، تعیین تعداد بهینه دیگها برای تأمین پایدار بخار در ساعات اوج مصرف، دورههای تعمیرات یا بارهای فصلی است که با تحلیل دقیق الگوی بار مصرفی مشخص میشود.
دیگهای بازیافتی : بهرهوری از گرمای دورریز
یکی از شیوههای مدرن در تولید بخار، استفاده از گرمای تلفشده در فرآیندهای صنعتی است. بهطور مثال، گازهای داغ خروجی از توربینهای گاز یا موتورهای احتراقی میتوانند بهجای هدردهی، به دیگهای مخصوصی هدایت شوند که به آنها «دیگ بازیافت حرارت» گفته میشود. این سیستمها بدون نیاز به سوخت اضافی، با بازیابی گرمای خروجی، بخار تولید میکنند و نقش مهمی در کاهش مصرف انرژی و هزینهها دارند.
افزایش راندمان با پیشگرمایش آب تغذیه
در بسیاری از طرحها، از آب بازیافتی ناشی از سامانههای خنککاری موتور یا کندانسور بهعنوان منبع آب پیشگرمشده استفاده میشود. این کار باعث کاهش زمان راهاندازی دیگ، مصرف سوخت کمتر و عملکرد پایدارتر آن میشود. اما چون عملکرد دیگهای بازیافتی در مواقعی به تنهایی پاسخگوی بار کامل نیست، معمولاً یک دیگ بخار کمکی در کنار آن نصب میشود تا در مواقع اوج مصرف یا قطع جریان گازهای داغ، بتواند کمبود بخار را جبران کند.
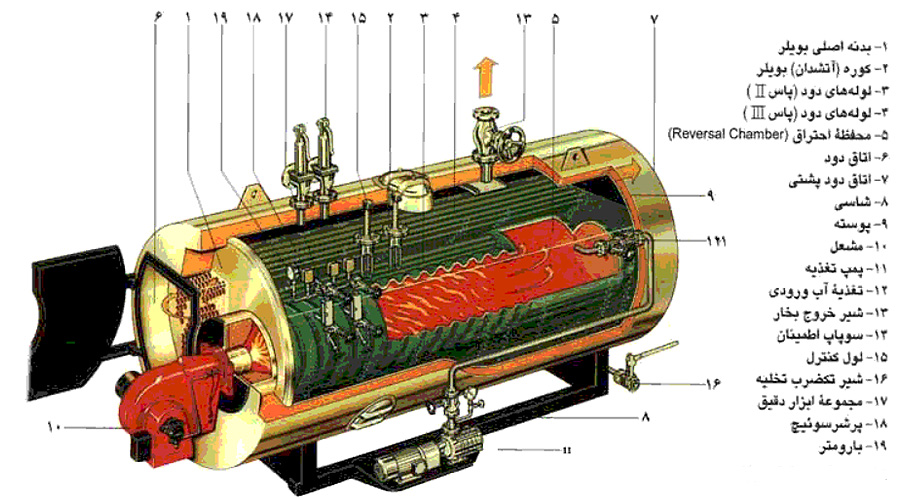
لولهکشی رفت دیگ بخار: حرکت کنترلشده بخار
در سیستمهای بخار کوچک، معمولاً یک خروجی اصلی برای بخار کافی است، مشروط بر آنکه قطر این خط خروجی طوری انتخاب شود که سرعت بخار زیاد بالا نرود. دلیل این مسئله کاهش احتمال کشیده شدن قطرات آب به خطوط بخار است که میتواند باعث ضربات قوچ یا آسیب به تجهیزات شود. در دیگهای بخار با ظرفیت بالا، استفاده از چند خروجی بخار بهصورت همزمان رایج است که موجب پایداری در فشار و توزیع بهتر بار سیستم میشود.
برخی مهندسان برای داشتن حجم ذخیره بخار بیشتر، اقدام به طراحی هدرهای بخار با قطر بالا میکنند، اما اگر تقاضای لحظهای بالا وجود نداشته باشد، این کار میتواند منجر به نوسانات کنترلنشده یا اتلاف انرژی شود. اندازهگذاری خطوط رفت بخار باید بر مبنای حداکثر بار مصرفی مورد انتظار، نه میانگین، انجام گیرد. همچنین هرگونه تغییر قطر لوله در مسیر، بایستی با اتصالاتی مانند زانوی کاهنده (Reducer Elbow) به شکلی اصولی صورت گیرد تا از اختلال در جریان جلوگیری شود.
لولهکشی برگشت : بازگشت بهینه کندانسیت به دیگ
در دیگهای چدنی، انعطافپذیری در محل برگشت آب وجود دارد و میتوان برگشت را از هر سمت دیگ انجام داد. در مقابل، در دیگهای فولادی معمولاً یک یا دو نقطۀ مشخص برای برگشت در نظر گرفته میشود. چنانچه دو ورودی برگشت طراحی شده باشد، استفاده از هر دو نقطه به بهبود جریان داخلی و ممانعت از مناطق داغ یا سرد داخل دیگ کمک شایانی میکند.
بازگشت کندانسیت میتواند به روش ثقلی یا با کمک پمپ انجام شود، اما برای سیستمهای حرفهای معمولاً از پمپ استفاده میشود تا کنترل دقیقتر و برگشت سریعتر اتفاق بیفتد. در این ساختار، هر دیگ میتواند پمپ مجزا داشته باشد یا از یک پمپ مرکزی برای تغذیۀ چند دیگ از طریق مانیفولد استفاده شود. در سناریوی دوم، شیرهای کنترلی متصل به سنسورهای سطح آب هر دیگ، مسیر مناسب را بهصورت خودکار باز و بسته میکنند تا توزیع آب کاملاً هوشمند انجام شود.
الزامات طراحی قطر لولههای برگشت
قطر لولههای برگشت نباید بهصورت تجربی یا ساده در نظر گرفته شود، بلکه باید بر اساس بار کل سیستم و حداکثر دبی طراحی گردد. بهویژه در خط لولهای که از پمپ تا دیگ کشیده میشود، افت فشار باید حداقلی باشد تا از کاهش راندمان و استهلاک زودرس پمپ جلوگیری شود. همچنین این خطوط باید توانایی تحمل فشار دائمی ناشی از عملکرد مداوم پمپ برگشت را داشته باشند.
ویژگیهای حیاتی آب تغذیه دیگ بخار
آبی که به دیگ بخار تزریق میشود، نباید تنها از نظر ظاهری پاک به نظر برسد، بلکه باید استانداردهای دقیق شیمیایی و فیزیکی را پشت سر گذاشته باشد. یکی از پرتکرارترین روشهای تصفیهای که برای آمادهسازی آب تغذیه به کار میرود، استفاده از سختیگیرهای رزینی با عملکرد کاتیونی در چرخه سدیمی است. این سختیگیرها پس از اشباع شدن با یونهای کلسیم و منیزیم، با آبنمک احیا شده و دوباره آماده بهرهبرداری میگردند.
کنترل کیفی : ضرورتی فراتر از توصیه
صرف استفاده از سیستمهای تصفیه کافی نیست؛ آب تغذیه باید بهطور مرتب مورد آزمایش قرار گیرد تا نتایج حاصل، با جداول استاندارد مقایسه شده و صحت عملکرد سیستم تأیید شود. این کنترل مستمر، ضامن عملکرد بینقص دیگ بخار و جلوگیری از خوردگی یا رسوبگذاری مخرب است.
دیاِریتور؛ مدافع بیصدا در برابر خوردگی
وجود گازهایی مثل اکسیژن و دیاکسیدکربن در آب تغذیه، اصلیترین علت خوردگی تجهیزات تحت فشار در بویلرهاست. دستگاه دیاِریتور بهعنوان یک سیستم هواگیری فیزیکی خارج از دیگ، این گازهای مضر را قبل از ورود آب به سیکل حذف میکند. با این کار، شرایط آب بهگونهای تنظیم میشود که محیطی قلیایی و احیاکننده ایجاد شود؛ محیطی که خوردگی در آن تقریباً غیرممکن میشود.
ترکیب هوشمندانه : هواگیری و افزودنی شیمیایی
در شرایط خاص یا برای افزایش سطح اطمینان، فرآیند دیاِریتینگ را میتوان با تزریق مواد شیمیایی مکمل کرد. این ترکیب همزمان، یک لایه امنیتی مضاعف ایجاد میکند که در برابر خورندگی مقاومت بالایی دارد.
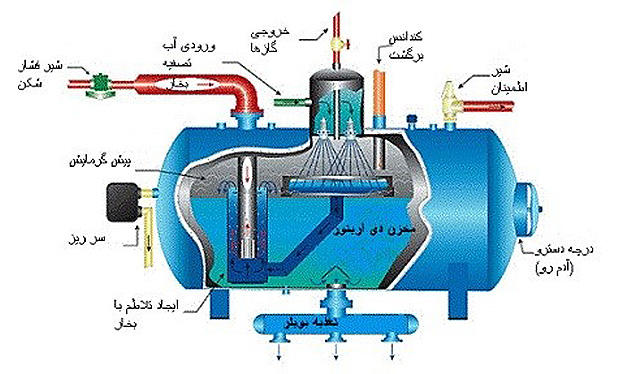
سوپرهیتر؛ افزایش دمای بخار، بدون افزایش فشار
برای ارتقاء بازدهی سیستم بخار و کاهش فشار مورد نیاز در دیگ، از واحدی به نام سوپرهیتر استفاده میشود. این تجهیز، بخار خروجی از بویلر را تا دمایی فراتر از نقطه جوش آب گرم میکند، بیآنکه فشاری اضافی به دیگ وارد نماید. نتیجه این کار، بخاری خشک، پُرانرژی و کارآمد برای مصرفکننده است.
اکونومایزر؛ هنر بازیابی انرژی پنهان
اکونومایزر یک مبدل حرارتی هوشمند است که در مسیر گازهای داغ خروجی از دیگ نصب میشود. این گازها پیش از خروج از دودکش، از این تجهیز عبور کرده و حرارت باقیمانده خود را به آب تغذیه منتقل میکنند. این پیشگرمایش باعث میشود آب ورودی با دمایی نزدیکتر به دمای عملکرد دیگ وارد سیستم شود، که این امر راندمان کلی را بالا برده و از شوک حرارتی یا خوردگی ناشی از دمای پایین جلوگیری مینماید.
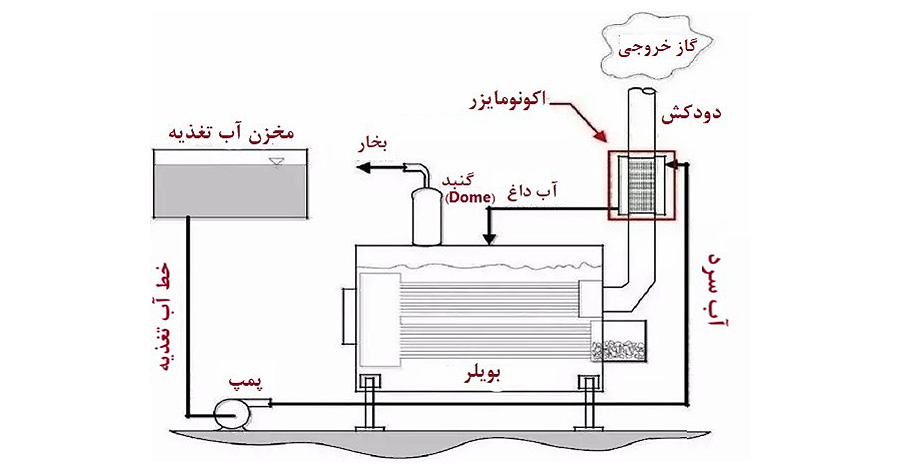
تولید بخار : منابع و روشهای متنوع
فرآیند تولید بخار میتواند به صورت مستقیم یا غیرمستقیم انجام شود. در روشهای مستقیم، دیگ بخار با سوزاندن سوختهایی مانند گاز طبیعی، گازوئیل، ذغال سنگ یا حتی چوب، انرژی حرارتی لازم را فراهم میکند. همچنین در برخی از صنایع، از انرژیهایی همچون الکتریسیته، نور خورشید یا حتی انرژی هستهای برای این منظور استفاده میشود. در مقابل، بخار را میتوان بهصورت غیرمستقیم نیز تولید کرد، بهویژه از طریق بازیافت گرمای اتلافی حاصل از تجهیزات و فرآیندهای صنعتی مانند موتورهای احتراقی یا توربینهای گازی.
بخار در ترکیب با تولید توان و گرمایش
در شرایطی که تأمین پیوسته بخار در تمام طول سال الزامی است، طراحی سیستم باید به گونهای باشد که قابلیت تولید همزمان بخار و برق را فراهم کند. در سیستمهای ترکیبی، بخار ابتدا برای چرخاندن توربینهای بخار و تولید الکتریسیته استفاده شده و سپس بخار خروجی که هنوز دارای انرژی گرمایی بالایی است، برای مصارف گرمایشی مانند سیستمهای حرارتی ساختمان یا فرآیندهای صنعتی بهکار گرفته میشود. این نوع بهرهوری دوگانه، یکی از اصول اساسی در طراحی نیروگاههای حرارتی مدرن محسوب میشود.
مدیریت بخار در سیستمهای بسته
در سامانههایی که بخار توسط دیگ بخار تأمین میشود و کندانسیت به چرخه بازمیگردد، باید تلاش شود که آب برگشتی تا حد ممکن گرم باشد تا از مصرف انرژی اضافی جلوگیری شود. اما همین گرما میتواند در نقطه مکش پمپ مشکلساز شود. بهویژه اگر دمای کندانسیت بیش از حد بالا باشد، ممکن است پدیدهی کاویتاسیون رخ دهد که به عملکرد پمپ آسیب میزند. بنابراین، برای محافظت از پمپ و پایدار نگهداشتن سیستم، بخشی از انرژی حرارتی باید گرفته شده و آب تا چند درجه زیر دمای اشباع خنک گردد؛ به این فرآیند اصطلاحاً "مادون سردسازی" (Subcooling) گفته میشود.
تفاوت سیستمهای باز و بسته در بازیابی انرژی
در بسیاری از تأسیسات شهری و نیمهصنعتی، چرخه بخار به صورت باز طراحی میشود، به این معنا که کندانسیت پس از استفاده به دیگ بازنمیگردد. در این شرایط، گرمای موجود در کندانسیت به نوعی اتلاف انرژی محسوب میشود. برای نمونه، اگر کندانسیت در دمای 180 درجه فارنهایت تولید و با کاهش دما تا 80 درجه بازیافت شود، حدود 10 تا 15 درصد از انرژی اولیه بخار هنوز در آن حفظ شده و قابل بازیابی است. استفاده از مبدلهای حرارتی برای بازپسگیری این انرژی، یکی از راهکارهای بهبود راندمان کلی سیستم است.
نتیجهگیری
آنچه در این بررسی تخصصی مشخص شد، این است که کیفیت آب تغذیه، تنها یک گزینه فنی نیست؛ بلکه سنگبنای امنیت، کارایی و دوام یک سیستم بخار صنعتی بهشمار میآید. دیگ بخار، با تمام پیچیدگیهای طراحی و مهندسیاش، بدون دریافت آب بهینه، تبدیل به نقطهای آسیبپذیر در زنجیره تولید میشود. ورود آب سخت، هواگیری ناقص، یا بخار اشباعشده با انرژی پایین، همگی میتوانند عملکرد کلی سامانه را دچار اختلال کرده و زمینهساز افت راندمان، توقف تولید، و حتی خرابیهای پرهزینه شوند.
راهکارهایی مانند بهرهگیری از دیاِریتور برای حذف گازهای خورنده، استفاده از سوپرهیتر برای تولید بخار خشک، یا نصب اکونومایزر بهمنظور بازیابی حرارت پنهان، صرفاً ابزارهای مکمل نیستند؛ بلکه سیاستهای هوشمندانهای هستند که بین بهرهبرداری صنعتی و مصرف انرژی تعادل برقرار میکنند. در کنار آن، طراحی اصولی مسیرهای رفت و برگشت بخار، انتخاب صحیح قطر لولهها و نوع پمپها، تضمینکننده بازده پایدار در بلندمدت است. در نهایت، آگاهی، طراحی علمی و کنترل مستمر، سه ضلع مثلثی هستند که هر سامانه بخار موفق بر آن استوار است. بیتوجهی به هر یک از این اضلاع، تنها به معنای کاهش راندمان نیست؛ بلکه میتواند به قیمت توقف تولید، آسیب به تجهیزات و زیانهای مالی جدی تمام شود.